ENVIRONMENTALLY FRIENDLY
The primary solutions utilized in the blacking process are of a water base, thus limiting safety and environmental hazards. Rinse water effluents are well within compliance of by-law guidelines of most municipalities.
EASY-TO-USE
Blackfast offers an extremely simple, easy-to use process for blacking iron & steel components in house at room temperature. The operator requires minimal training, and there is no prior chemical knowledge required.
ECONOMICAL
The processing of parts costs pennies a piece! Products are long lasting and can sit for long periods of time and be ready to go when you have work to process. Topped up, not disposed of, reducing overall costs.
The Blackfast Process
The traditional procedure for Black Oxide was to send your parts out to a metal finishing house. This resulted in complications, wait time and expense.
e-Black Solutions presents an alternative solution that actually works!
WHY DO YOUR OWN IN-HOUSE BLACKING?
Reduce down time.
Avoid sending out for hot black oxide.
Can be carried out by junior staff requiring no chemical knowledge.
Avoid incurring shipping and handling costs.
Wasted time tracing outsource items.
Loss of control of your own productivity.
In-House Quality Control.
Consistent deep black finish.
No more creeping white salt corrosion.
THE WILLs AND WILL NOTs OF BLACKING
Blackfast will blacken:
Any ferrous metal; carbon steel, mild steel, tool steel, high speed steel. Steel hardened to 60 Rockwell. Steel with less than 12% nickel or chrome content; surface hardened items.
Cast iron, ductile iron, forged steel.
Blackfast will not blacken:
Stainless steel, rust resistant metals, brass.
Metals great than 12% nickel or chrome, metals harder than 60 Rockwell.
Metals with any trace of oil or rust inhibitors or red rusted metals.
NO DIMENSIONAL CHANGE
The converted black surface is between 1.5 and 3 microns in thickness.
The degree of thickness is proportionate to the degree of microscopic variance in the machined surface prior to blacking. The surface conversion actually corrects some microscopic imperfections in the component.
There is no change to the hardness of the material.
The chemical description of the process is “an Inert Copper Selenoid Phosphate”.
Think of a nut and bolt. You can’t thread something dimensionally changed.
CORROSION PROTECTION
The Blackfast process provides corrosion protection that surpasses that of the traditional hot black oxide method, due to the microcrystalline converted surface.
Long lasting humidity barrier which hampers oxidation.
Testing resulted in no corrosion after 244 hours of humidity cabinet exposure & significant corrosion only after 48 hours of salt spray, using our standard 833C dewatering oil.
Traditional Hot black oxide test results typically range from 48 to 120 hours humidity cabinet only.
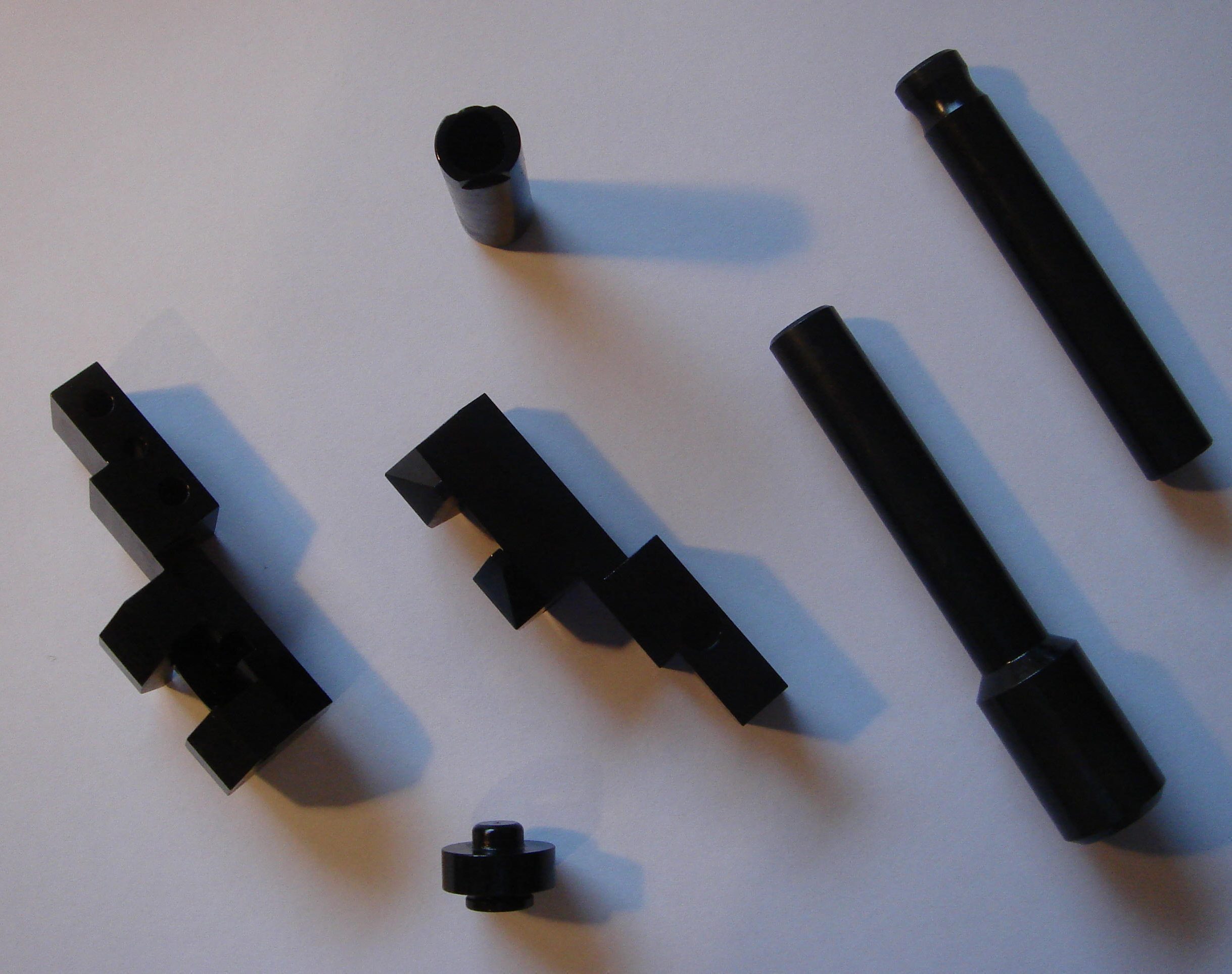
Company Profile
Enjoy the best:
Customer ServiceTechnical SupportProduct SatisfactionGuarantee of QualityAvailability of servicePricing & much more.
Warehouses are located in both Canada & the United States of America to serve you better.
e-Black Solutions is proud to represent the manufacturer, Blackfast Chemicals Ltd., UK. as the North American Distributor of Blackfast Room Temperature Blacking Products.
We are currently in our 22nd year of service.
Our administrative office is located in Brantford, Ontario, Canada
We have state of the art warehouse facilities in Milton, Ontario, Canada and Buffalo, New York, USA where orders are prepared and shipped within one business day. Delivery time in transit varies by location.
We are partnered with FedEx Ground Service for reliable, cost-effective and damage free deliveries. Trucking LTL logistics are provided upon request.
Blacking Kits
Small Blackfast Systems are 20 litre (5.28 US Gal.) of working chemical and are available as chemical only or complete with chemical & pails. Quotes are available for larger production scales systems or large chemical orders. Please inquire.
PRODUCT DESCRIPTION
10 litres of 716C Light Alkaline Cleaner
5 litres of 551 Conditioner
5 litres of 181 Blacking Agent
20 litres of 833C Dewatering Oil/Inhibitor
1 set of tank labels & thermometer strips
TOTAL (Chemical only)
TOTAL (Complete, chemical + Pails @ $84.50)
Processed on Visa or Mastercard in $CAD
+ $75.00 shipping & handling charges for Ontario, higher for other provinces. HST extra & a credit card processing fee of 1.75%
CANADIAN PRICING IN $CAN
$125.00 (2 x $62.50 per 5L)
$115.99
$146.01
$227.50
Free
$614.50+
$699.00+
PRODUCT DESCRIPTION
10 litres of 716C Light Alkaline Cleaner
5 litres of 551 Conditioner
5 litres of 181 Blacking Agent
20 litres of 833C Dewatering Oil/Inhibitor
1 set of tank labels & thermometer strips
TOTAL (Chemical only)
TOTAL (Complete, chemical + Pails @ $80.00)
Processed on Visa or Mastercard in $USD
+ Full shipping & handling charges from Buffalo, NY USA & a credit card processing fee of 1.75%
U.S.A. PRICING in $USD
$109.00 (2 x $54.50 per 5L)
$103.50
$129.50
$187.25
Free
$529.25+
$609.251+
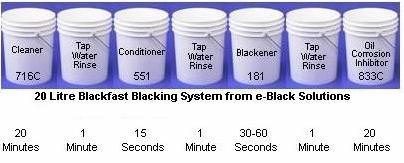
Blackfast TV
The Small Blackfast System has 716C Cleaner, a water rinse, 551 Conditioner, a water rinse, 181 Blacking Agent, a water rinse, 833C Dewatering Oil & Air dry. The system can be enhanced with flowing, agitated water and heated 181 Blacking. Click below to watch in YouTube.
The Production Scale Blackfast System has 626 Hot Cleaner, a static water rinse, an agitated, flowing water rinse, 551 Conditioner, an agitated, flowing water rinse, heated 181 Blacking Agent, an agitated, flowing water rinse, heated 933 Emulsion Oil & Air dry. Rinse water recycling can be omitted if desired. Click below to watch in YouTube
Literature
Printable website
Do you want a complete copy of our website? Simply click on the link below and view, save or print it in .pdf
MSDS / SDS (GHS) / NFPA Information
Material Safety Data Sheets (MSDS) have been replaced with Safety Data Sheets in a Global Harmonized System or SDS (GHS).
The National Fire Protection Association (NFPA) is a color coded system for safety handling.